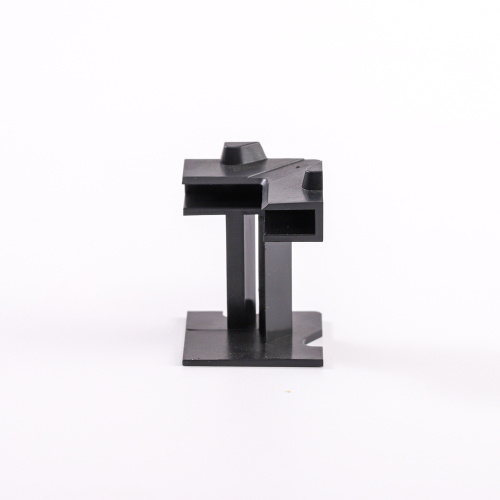
Custom plastic mould design
- Min. Order:
- 1000 Piece/Pieces
- Min. Order:
- 1000 Piece/Pieces
- Transportation:
- Ocean, Land, Air
- Port:
- Shanghai
Your message must be between 20 to 2000 characters
Contact NowPlace of Origin: | China |
---|---|
Productivity: | 10000000 |
Supply Ability: | 1000000 |
Payment Type: | L/C,T/T |
Incoterm: | FOB |
Transportation: | Ocean,Land,Air |
Port: | Shanghai |
Custom plastic mould design:
1. Product design: The first step in custom plastic mould design is to create a product design. This design will serve as a blueprint for the mould design.
2. Mould design: Once the product design is finalized, the mould design process can begin. The mould design will include the shape and size of the mould, the number of cavities, and the placement of the injection points.
3. Material selection: The type of plastic used for the mould will depend on the product design and the intended use of the final product. The material must be able to withstand the injection molding process and the final product must meet the required specifications.
4. Prototype creation: A prototype of the mould is created to test its functionality and identify any design flaws.
5. Production: Once the prototype has been approved, the final mould is created and used for production.
6. Quality control: Quality control measures are implemented to ensure that the final product meets the required specifications.
Overall, custom plastic mould design requires careful planning, attention to detail, and expertise in the injection molding process. It is important to work with an experienced and reputable manufacturer to ensure the best results.
Our R & D department has 6 professional engineers, can provide customers with mold and product design engineering and technical design support. We have more than 10 years of production experience, strict process to control the quality and time of production, to provide you with high quality and punctual delivery. We are a manufacturer of moulds and molded parts, which helps our customers save money. As you know, there is no lowest price, only reasonable price. We can carry out assembly, printing, painting, decoration and other secondary operations when needed. Our plant and equipment currently has 15 molding machines ranging from 80 tons to 300 tons. We have won the good reputation and trust of our customers. We provide from plastic injection mold design - injection mold 3D drawing - mold processing - injection mold manufacturing - processing - surface treatment - packaging and other one-stop services.The company has a wide range of injection molding products, the main products are mobile phone shell, refrigerator plastic shelf, projection TV back shell, plastic light box, plastic words, plastic bags, plastic cups, car dashboard accessories, seat back accessories, car door accessories, toy car shell, etc. I can also design injection moulds, Plastic Bottle Mould Design,Custom-made Plastic Part Mould, Injection Tooling & Mold Design
1. Determine the part requirements: Before designing the mould, you need to know the part requirements such as the size, shape, and functionality of the part.
2. Select the appropriate plastic material: The plastic material you choose will determine the mould design. Factors such as the melting temperature, shrinkage, and flow rate of the plastic should be considered.
3. Choose the mould type: There are different types of moulds such as injection moulds, blow moulds, and compression moulds. The mould type you choose will depend on the part requirements and the plastic material.
4. Custom plastic mould design: The mould design should include the part geometry, gating system, cooling system, and ejection system. The gating system is the channel through which the plastic flows into the mould cavity. The cooling system is necessary to control the temperature of the mould during the injection process. The ejection system is responsible for removing the part from the mould.
5. Test the mould: Once the mould is designed, it should be tested to ensure that it meets the part requirements. The testing process may involve making a prototype or a small batch of parts to check for any defects.
6. Make adjustments: If any defects are found during testing, adjustments should be made to the mould design. This may involve modifying the gating system, cooling system, or ejection system.
7. Production: Once the mould is tested and adjusted, it can be used for production. The mould should be regularly maintained to ensure that it continues to produce high-quality parts.
Competitive Advantages:
1. In the field of electronic products, we have long-term cooperation with some of the world's top brands, such as Epson,
Canon and SONY.
2. The company has successfully passed ISO9001 quality management system and IGS quality management system certification.
3. We can design and manufacture molds of different specifications and standards, such as DME,HASCO
And DAIDO.
4. Our factory is equipped with the most advanced testing instruments to effectively ensure the accuracy
The mold.
5. Strict quality control;
6. Good after-sales service;
7. Deliver on time
Related Keywords