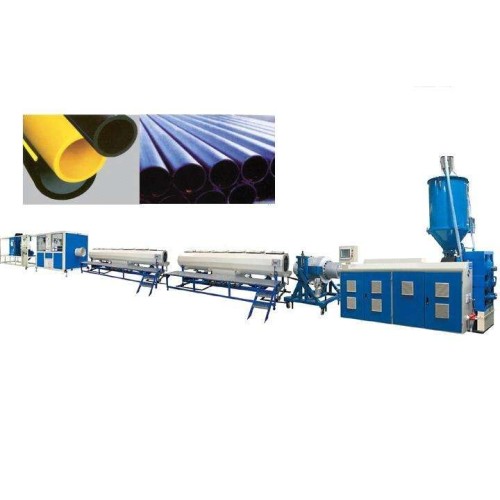
PP Pipe Extrusion Line with High Output 1200kG/H
- Transportation:
- Ocean, Land
- Port:
- Shanghai
Your message must be between 20 to 2000 characters
Contact NowPlace of Origin: | JIANGSU, CHINA |
---|---|
Payment Type: | L/C,T/T,D/P,Western Union |
Incoterm: | FOB,CIF,EXW,CFR |
Certificate: | CE |
Transportation: | Ocean,Land |
Port: | Shanghai |
PP Pipe Extrusion Line with High Output 1200kG/H
CHARACTER & APPLICATIONS OF PP PIPES
The Raw material, Polypropylene (PP) is a kind of partly crystalline thermoplastics which is similar to HD-PE. Compared with HD-PE, it has the features of higher stiffness, strength, and hardness levels. One of the significant character of PP is its excellent chemical resistance. The PP Pipes can be used for chemical industry. It can handle with the aggressive waste water, even the water are used at high temperature. Because Polypropylene can be used in temperatures up to 95 °C. However, below the freezing point, PP is very sensitive and vulnerable.
ADVANTAGES OF PP PIPES
- Safety of potable water and long-term reliability
- Resistance to corrosion, tuberculation, deposits
- Chlorine and chloramine resistance
- Lightweight, easy to transport
- No scrap value, avoiding jobsite theft
- Durability and toughness to survive jobsite installations
- No flame, glue or solders are used for joining, heat-fused joints
- Available in wide range of sizes
- Natural Insulator, low thermal conductivity
- Professional installed appearance
PRODUCTION PROCESS FLOW
The first step of pipe production is the preparation of raw material. Customers can mix the PVC powder with other additives by themself. The mixture will be feeded into extruder. The material will be plasticized in the extruder and then be extruded into the mould. The material is shaped by mould and goes out with the pipe looking. The pipe extruded from the mould is hot and soft. The pipe with unstable shape will be calibrated and cooled by vacuum sleeve in the vacuum calibration tank. And then the pipe goes into the cooling tank for a further cooling. Haul off unit stands next to the cooling tank and take the pipe away from the extruder. According to the defined length, the pipe will be cut and then packed for transport.
FEATURES OF PRODUCTION LINE
In order to meet the customized production plan, various design concepts for equipment will be adopted. Basically feeding system, conical twin-screw extruder, mould, vacuum calibration tank, cooling tank, haul-off machine, cutter, socket forming machine (optional) and stacker build up the complete production line.
For a stable production with high performance, we have a mature solution package, which involves design concept, manufacturing and assembly process. It can eliminates many potential risks during production. The Core components such as motor and frequency inverter are chosen from the world famous brand, which guarantees a precise and reliable production.
If you want a customized production plan, please contact us to get more detailed information.
INTRODUCTION OF COMPONENTS
-
Single screw Extruder
Screw and barrel are produced by professional factory with good quality. With Siemens Motor and ABB frequency inverter the Driving unit guarantees a long term stable running. Heating method is chosen by Electric aluminum cast heating element.
- Mould
The Mould shapes the melting material to pipe form. The designing of our mould provides ideal viscosity of material melting, which influences the pipe shaping and extrusion energy. All faces in contact with material are polished, so that the extrusion frication can be minimized.
-
Vaccum Calibration Tank & Cooling Tank
Through the Vacuum Calibration Tank, the pipe shape will be defined. Besides that the surface quality of pipes is influenced by this step. The Cooling water sprinkles on the hot plastic pipe surface. Combined with the shaping of the mould the surface quality of pipes will be defined.
Our vacuum tank’s pressure can be adjusted, so vacuum pressure can be fixed according to pipe requirement. We sealing gasket for every lid on the vacuum tank. This stops vacuum leakage and minimizing energy consumption.
- Haul off Unit
A wide range of haul-off units allows us to supply to the customers the ideal solution for a large diameter range.
Caterpillar and Belt Haul-off units can be adopted according to the production condition.
Haul-off speed can be connected with the extrusion speed, so that the wall thickness are more symmetrical.
The Belt Haul-off unit is usually used for small pipe and high speed extrusion. It is free from vibration and ensure the excellent control even at high speed.
The Caterpillar can take the big pipe easily. The Claws' surface is covering with foam PU. This can prevent the slip between pipes and claws.
The speed setting of belts and caterpillar can be
adjusted by inverter and man operates on the control panel easily.
- Cutter
A cutter with high performance can ensure the same length of the cut Pipes. So the high quality encoder and precise cutter unit are needed. Similar like Haul off unit, the cutter has two design concept: saw cutter and planet saw cutter. It depends on the diameter of to cut pipe.
- Control system
The Control system includes the whole operations related controller and executor such as PLC module, HMI panel (Human Machine Interface), thermometer, connector and so on. The Elements with high quality is significant for a stable and precise production.
- optional unit
For Pipe Production, there are some functional unit like laser/ ink printer and pipe stacker
With Printer the production information will be printed on the Pipes.
Stacker collects the pipes after cutting.
Related Keywords