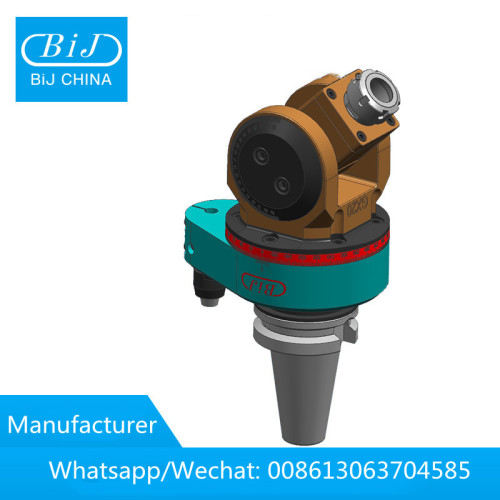
Angle Head for VMC
- Transportation:
- Ocean, Land, Air, Express
- Port:
- Shanghai
Your message must be between 20 to 2000 characters
Contact NowPlace of Origin: | China |
---|---|
Payment Type: | T/T |
Incoterm: | FOB,CIF,EXW,CFR,Express Delivery |
Transportation: | Ocean,Land,Air,Express |
Port: | Shanghai |
We mainly produce all kinds of angle head for CNC machining center, CNC gantry milling machine, gantry type milling machine vertical milling machine, vertical drilling and tapping machine.
BiJ is a professional manufacturer providing one-stop service. More than ten years of experience in Angle head design, production and after-sales service. From communication and selection to processing and production, and then to post-programming guidance, we provide customers with complete Angle head solutions.
For milling cutters with tapping teeth above M16 and tool diameters above φ20, greater locking force should be applied to the collet nut. The length of the milling cutter should not be too long, and the processing should be matched with the appropriate speed and feed, otherwise it will produce serious shock. If the Angle head is damaged and cannot be used, please ask the dealer of angle milling headsfirst. Do not try to repair it by yourself
Parameter:
PRM----3000RPM Torsion-----60NM
Clamp Range: 3-20mm Tapping: Biggest M16(S45C)
Gear Ratio: 1:1
Material: Steel
Inspection: 100% Inspection before shipping to ensure the quality.
Model no: BT50-ER32-ANG195
Our production drawing below:
Installation of cnc angle head
Check the hex screws of the locking ring. They are locked. Loosen the side locking screw of the positioning pin and press the positioning pin to the lowest height before locking the side locking screw. Loosen the side setting screw of the stop ring to allow the shank to rotate freely.
Wipe the spindle mounting surface of the machine tool clean, remove the screws needed on the spindle (the positioning block should be installed in the non-interference position of the spindle tool change arm as far as possible), lock the positioning block on the spindle mounting surface, and appropriately increase the locking force to ensure the locking degree.
Position the M19 spindle of the machine tool and check whether the inner cone hole of the machine tool spindle is clean. Put the Angle head into the spindle of the machine tool, find the relative position of the clamping slot and positioning pin of the Angle head and the spindle and positioning block of the machine tool. Push the Angle head into the spindle of the machine tool, and reciprocate several times to confirm that the Angle head stop block can spring back to the slot of the stop ring smoothly. Take down the Angle head to lock the side fixing screw of the ring circle, and increase the locking force to ensure that the lock is firm. Push the Angle head into the machine master again
Shaft, check that the stop can spring back into the stop ring slot smoothly.
Load the Latin, load the Angle head into the spindle of the machine tool and tighten it, then manually turn the spindle of the machine tool to check whether it is smooth. After the Angle head is loaded into the spindle of the machine tool, the stop block will leave the stop ring slot to the middle position, and the above and the below will not interfere. Loosen the side locking screw of the positioning pin, so that the positioning pin automatically springs back to the positioning block, so that the outer cone of the positioning pin and the inner cone of the positioning block fit without gap, and lock the side fixing screw of the positioning pin.
Loosen the locking screw of the Angle head holding ring, and then the Angle head body can be manually rotated horizontally 360 degrees. Use the calibration table to level the datum level, lock the locking screw of the Angle head holding ring, set the machine speed to 50 RPM, check whether there is any abnormality, set the spindle speed of the machine tool to 1000 RPM, and check again.
Related Keywords