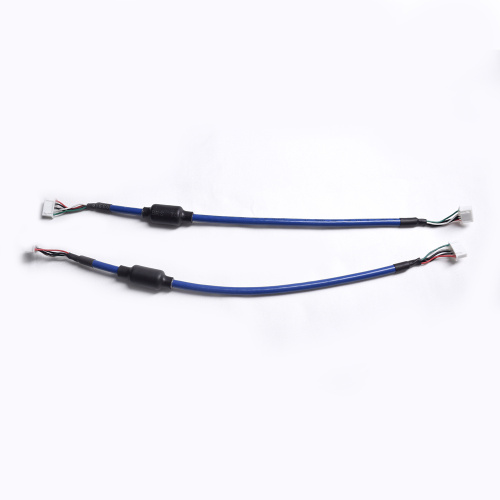
Custom Electronic Wiring Harness
- Min. Order:
- 500 Piece/Pieces
- Min. Order:
- 500 Piece/Pieces
- Transportation:
- Ocean, Land, Air, Express
- Port:
- Shanghai, Ningbo
Your message must be between 20 to 2000 characters
Contact NowPlace of Origin: | China |
---|---|
Productivity: | 10000000pieces/year |
Supply Ability: | 1000000pieces/month |
Payment Type: | L/C,T/T,D/P |
Incoterm: | FOB,CFR,CIF,EXW,DDP,DDU,Express Delivery |
Certificate: | UL.IPC620.REACH.ROHS2.0 |
HS Code: | 8544601200 |
Transportation: | Ocean,Land,Air,Express |
Port: | Shanghai,Ningbo |
Electronic cable assembly is relatively common and relatively simple custom wiring harnesses. Its production process has the following steps:
1. Wire cutting: Check whether the standard type of wire is correct and whether the size of the electronic harness meets the requirements.
2. Peeling: Check whether the peeling port is flat, and the core wire, braided wire, etc. cannot be peeled off, and whether the peeling scale is correct.
3. Grouping processing: whether the trimming scale is correct, whether the trimming is smooth, and the core wire cannot be damaged when trimming and grouping.
4. Peeling the inner skin: check whether the peeling port is flat; whether the peeling scale is correct; whether there is a peeled core wire and a broken copper wire; when half-peeling, the insulator cannot fall off.
5. Sleeve shortening tube: Check whether the shortening tube size and type are correct.
6. Preparation for welding: check whether the temperature of the tin furnace is correct; whether the core wire copper wire is arranged before welding, whether there are forks, twists, discounts, etc.; whether there are copper wire forks, large ends, uneven copper wires, insulating skin after welding Appearance of burns, etc.
7. Soldering: Check whether the temperature of the electric soldering iron is correct; the insulating skin should not be scalded, the tin point should be lubricated, no tin tip, and no false welding or false welding.
8. Terminal pressure: confirm whether the standard of the terminal and wire is correct; whether the terminal pressure has a flare, skew, and whether the insulation and core wires are too long or too short.
9. Terminal piercing: Check whether the terminal type is correct; whether the terminal is damaged, deformed, etc.;
10. Cable crimping: Check whether the connector type is correct; whether the cable direction is correct; whether the core wire is damaged, exposed copper, or burnt; is the crimping in place?
11. Blow and shorten the tube: whether the shortening tube is protruding, and the insulating skin cannot be scalded.
12. Assembling the shell: whether the shell is installed incorrectly, whether there are scratches, wool edges, etc., whether there are missing parts, whether the screws are twisted, oxidized, discolored, loose, etc., and do not meet the bad requirements after assembly; if the shell has Orientation, you must assemble as required.
13. Labeling: Check whether the content of the label is correct, clear, and without hyphenation; whether the label size is correct; whether the label is dirty or damaged; whether the label is posted in the correct direction.
14. Check whether the standard, color and direction of the cable tie are correct; there is no cracking or loosening.
15. Injection molding: Check whether there is dirt on the mold, and whether there is a lack of material, air bubbles, poor bonding, and poor hardening in the molding part.
16. Plug molding: Check whether the plug molding is damaged, uneven, lack of material, wool edges, debris, streamlines, etc., and admit that the metal terminals are not deformed, damaged, copper exposure, etc.
17. Electrical inspection: check according to the requirements of the inspection guide ticket of the corresponding product.
18. Visual inspection: As long as you can see it, pay attention to all items.
Wire harness production and processing are roughly these processes, and some are more complicated. Our factory is located in Suzhou, with advanced wire harness processing equipment and experienced wire harness engineers. Industrial wiring harness has always been our main product. Both our agricultural machinery navigation wire harness and drone wire harness have applications in agriculture. Now more and more vegetation protection work is slowly being replaced by drones, which saves time and effort than manual work. Also closely related to people's lives is the medical field. The medical devices used in hospitals are diverse and in great demand, especially disposable medical supplies. We have produced medical defibrillator wire harness and aid equipment wire harness. We are confident and capable of producing satisfactory customized wire harnesses for customers.
With the advancement of science and technology, the application of wire harnesses can be seen in the operation of the agricultural field, from the initial manual operation to the use of machinery, to the current pure mechanical operation. Our custom harnesses are all produced under the IPC620 standard. We also have the capability to manufacture Health equipment Wire Harness and Medical Power Harness.
Connector |
JST |
Rated voltage |
DC500V, 10 ms |
Product certification |
RV, IPC620, REACH, ROHS2.0, MASDS |
Wire |
UL2464 1P*24AWG+2C*24AWG+A+E+B |
Processing technology |
Stripping, welding, riveting, process assembly |
On-resistance |
≥20MΩ |
Insulation resistance |
≤2Ω |
Application field |
Consumer Electronic Cable Assembly |
Related Keywords