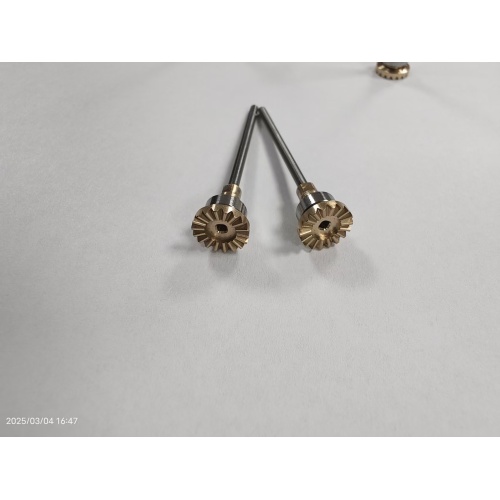
030.5 ball screw 3mm diameter 0.5mm pitch
Quantity:
Your message must be between 20 to 2000 characters
Contact NowBasic Info
Basic Info
Product Description
Product Description
The application of 030.5 ball screws in humanoid robots is a complex and multi-faceted technical choice. The following is a systematic analysis of its application scenarios, advantages, challenges and solutions:
The basic principle of ball screws
Structure and working principle: Composed of a lead screw, a nut and circulating balls, it converts rotational motion into linear motion through rolling friction and vice versa. Compared with traditional sliding lead screws, it has less friction and higher efficiency (usually > 90%).
High precision and load capacity: Suitable for scenarios requiring micron-level positioning (such as finger joints), and capable of withstanding high axial loads.
2. Typical applications in humanoid robots
Joint drive: Linear drive for knee or elbow joints, converting motor rotation into joint bending.
Dexterous finger operation: Precisely control the grasping force and position to adapt to different object shapes.
Balance adjustment: Enhance dynamic balance ability by quickly adjusting the position of the center of gravity (such as the hip or ankle).
3. Core advantages
High efficiency and energy conservation: Rolling friction reduces energy loss and extends battery life.
High rigidity: Supports heavy-duty joints (such as leg load-bearing structures) and reduces deformation.
Repeat positioning accuracy: Under closed-loop control, the error can be controlled within ±0.01mm, which is suitable for fine movements.
4. Challenges Faced and Solutions
Volume and weight:
Challenge: Large lead screws may increase the robot's own weight.
Solution: Adopt miniaturized design (such as a 6mm diameter lead screw) or lightweight materials (titanium alloy, carbon fiber composite materials).
Dynamic response
Challenge: The inertia of the nut affects the response speed during high-speed movement.
Optimization: Cooperate with high-torque density motors (such as frameless torque motors) and optimize the algorithm to achieve predictive control.
Environmental adaptability
Sealing and lubrication: Use IP67 grade sealing rings and long-lasting grease (such as perfluoropolyether grease), suitable for dusty or humid environments.
Temperature management: Design the heat dissipation structure through thermal simulation to avoid thermal expansion errors caused by high temperatures.
Cost and Maintenance
Cost reduction strategy: Large-scale production or the use of plastic ball nuts (such as POM material) to reduce costs in some load scenarios.
Extended maintenance cycle: Self-lubricating materials or condition monitoring systems (vibration sensors) enable predictive maintenance.
5. Comparison of alternative solutions
Harmonic reducer + belt/gear: Suitable for compact Spaces, but linear motion requires an additional conversion mechanism.
Linear motors: High speed and high precision, but high cost and electromagnetic interference needs to be dealt with.
Hydraulic drive: High power density, but complex and requires frequent maintenance.
6. Practical application cases
Boston Dynamics Atlas: Some versions are hydraulically driven, but the laboratory prototype explores ball screws for lightweight joints.
Toyota HSR robot: It uses ball screws in the arm extension mechanism to achieve millimeter-level grasping accuracy.
7. Future Trends
Intelligent integration: Built-in sensors (pressure, temperature) enable real-time health monitoring.
Material innovation: Ceramic balls or graphene coatings further reduce friction and wear.
Conclusion
Ball screws are suitable for high-precision and high-load linear drive scenarios in humanoid robots, but their design needs to be optimized around lightweight, environmental robustness and cost. In the future, with the advancement of materials and manufacturing technologies, its application potential in humanoid robots will be further unleashed.
Related Keywords
Related Keywords