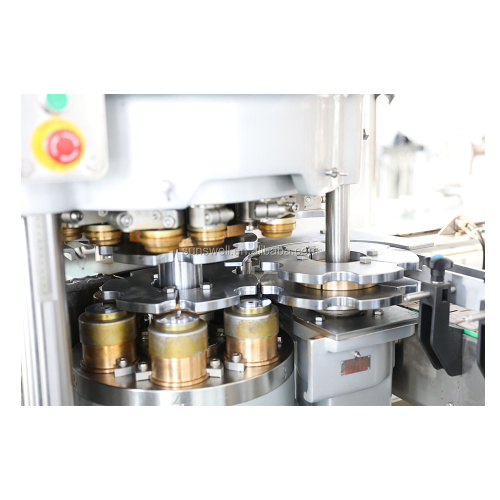
Aluminum Beer Beverage Can Filling Sealing Equipment Machine
-
$250000.00≥15000 Set/Sets
- Min. Order:
- 15000 Set/Sets
- Min. Order:
- 15000 Set/Sets
- Transportation:
- Ocean
- Port:
- shanghai
Your message must be between 20 to 2000 characters
Contact NowPlace of Origin: | china |
---|---|
Supply Ability: | 50 sets per year |
Payment Type: | L/C,T/T |
Certificate: | CE, ISO |
Transportation: | Ocean |
Port: | shanghai |
Machine characteristics:
Technical features of cans and cans: The cans are mainly used for the sealing of tin cans, aluminum alloys, plastics and other cans. It has the automatic stop device with cans without cover, no cans without cover, in and out cans and other faults. It is the ideal equipment for canned food factory, beverage factory and winery sealing. The cover portion seals the lid to the jar that has been filled with the product and is transported by the conveyor chain to the subsequent process. The sealing roller is quenched with high hardness alloy (hrc>62), and the sealing curve is precision machined by optical curve grinding to ensure the quality of the sealing and ensure the normal operation of the machine. This machine has a can bottom cover, no cans and no cover control system to ensure the normal operation of the machine and reduce the cover loss rate. The aluminum cover is manually placed in the chute by the cover gravity and the thruster for the lower cover, and the detection switch is installed in the chute to ensure that the cover can be stopped when the cover is missing. According to the tank type of different heights, the capping machine can be manually raised and lowered to meet the requirements.
Aluminum Can Filling Machine
Liquid Filling Machine,Bottle Filling Machine Manufacturer
1 Carbonation Mixer
General Introduction
QHS series beverage mixer has the reasonable structure, high precision mix, plenty CO2 mix. Mainly applies to all carbonated beverages mixed processing, and can also be used for other beverages. It is the main equipment in complete equipments of carbonated beverage manufacturing.
Main features
1) Advanced mass flow in-line blending and carbonation for reduced product & ingredient losses;
2) High efficiency deaeration
3) Simplified, user-friendly, operator interface
4) Automated “ no-dump” start-up capability
5) Complete product recipe management
6) Ingredient usage trending and totalling
7) Improved product yields and consistency
8) Reduced B.O.D. cost
9) Fast, favorable return-on-investment
Aluminum Can Filling Machine
Process
Automatic Bottle Water Filling Line
Water De-aeration Water Carbonation Proportioning of water and syrup Cooling System
Bottle Filling Machine
Beverage Filling Machine
China Water Bottling Machine Small
2 Depalletizer

General Introduction
QHS series beverage mixer has the reasonable structure, high precision mix, plenty CO2 mix. Mainly applies to all carbonated beverages mixed processing, and can also be used for other beverages. It is the main equipment in complete equipments of carbonated beverage manufacturing.
Main features
1) Advanced mass flow in-line blending and carbonation for reduced product & ingredient losses;
2) High efficiency deaeration
3) Simplified, user-friendly, operator interface
4) Automated “ no-dump” start-up capability
5) Complete product recipe management
6) Ingredient usage trending and totalling
7) Improved product yields and consistency
8) Reduced B.O.D. cost
9) Fast, favorable return-on-investment
Process
Water De-aeration Water Carbonation Proportioning of water and syrup Cooling System
2 Depalletizer
Model |
XD200 |
Production capacity |
12000 cans/hour |
Applicable bottle |
cans |
Compressed air consumption |
0.01M3 /min , 6~8bar |
Operating voltage(AC) |
380V |
Control voltage(DC) |
24V |
Total power |
6.37KW |
Total weight |
5000kg |
3 Can Rinser
General description
It is used to clean empty can in canning production line. Empty cans will be sent to turning device first, which will be turned around then transferred into rinsing machine. Empty can will be running from top to bottom along the turning device. When empty cans enter into rinser, they will be cleaned by 80ºC hot water (provided by customer) to reach aseptic state of can. There is certain inclination angle in both sides of rinser, whose size could be adjusted properly when needed. Empty cans will be rolling in parallel way from top to end; the waste water will be discharged from outfall.
Technical parameters
Required capacity |
0-200 CPM (330ml) |
Diameter of Can |
53~66mm |
Height of Can |
70~175mm |
Dimensions |
6200×470×310mm (L×W×H) |
Machine weight |
500Kg |
4 Can Filler/Seamer Monoblock
Description
It is suitable for filling and seaming carbonated liquid such as cola, beer, functional beverage, etc. It is equipped the advanced device, electrical equipment, and pneumatic control technology. It has the characteristics of filling reposefully, high speed, liquid level control, seaming reliably, frequency conversion timing, less material loss. It is the preferred equipment for beverage plants.
Features
Wholly sealed widow structure which is beautiful, concise, easy and highly operated;
Product tank design with precision polishing inside;
High precision and large flow rate filling valves to meet productive requirement;
Specially designed roller structure which is easy to be adjusted, locked and ensure sealing function;
Friendly and convenient operating panel with high expansibility.
Working Procedure
Cans will be pushed into can holding platform one by one by feeding screw and star-wheel. Centering cup of filling valve will fall to can; the distance between filling valves and cans is sealed by springiness plastic ring. The movement of centering cup is generated by plastic idler wheel along curvilinear motion. After filled, valve will be closed and centering cup will rise from the can. Filled can will be sent to conveyor chain, then to seamer. Seamer will take lid, turn over the edge of can and turn the edge to finish the sealing action by the control of cam. After that can will be transferred to conveying system.
5 X-ray Level Detector
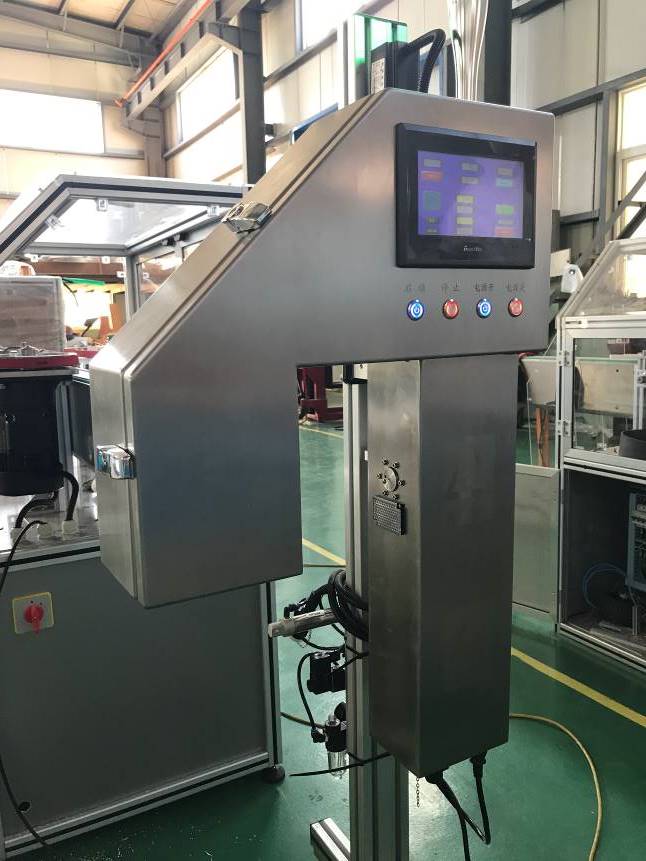
Description
Filling level detector is developed to meet international advanced level liquid level detection requirements. Use of low-energy X-ray after the interaction with the tested substances, materials-ray intensity with the test material surface changes the position of principle, to control the detection of liquid filling material capacity. Because of its non-contact measurement, a fundamental solution to the conventional weighing method cannot measure the liquid filling material on the production line capacity problems. It is widely used in food, pharmaceutical, chemical and other filling (either bottled or canned) liquid-line automatic control of the pipeline material. For ensuring product quality, increase economic efficiency and social significance.
Related Keywords