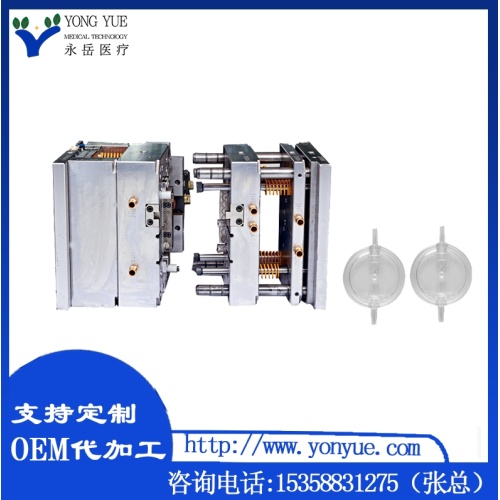
Precision mold for filters
-
$10000.00≥1 Set/Sets
- Min. Order:
- 1 Set/Sets
- Min. Order:
- 1 Set/Sets
- Transportation:
- Express
- Port:
- SHANGHAI
Quantity:
Your message must be between 20 to 2000 characters
Contact NowBasic Info
Basic Info
Transportation: | Express |
---|---|
Port: | SHANGHAI |
Product Description
Product Description
In today's highly industrialized era, filters play an indispensable role in various fields, ranging from air intake filtration in automotive engines to liquid filtration in medical equipment, from air purification in industrial production to water filtration in household water purifiers. The quality and performance of filters largely depend on the molds used in their manufacturing process - filter molds.
The design of filter molds is a challenging and technical process. Designers need to comprehensively consider numerous factors such as the application of the filter, filtration accuracy requirements, fluid characteristics, and working environment. Take the mold for automotive engine oil filters as an example. It is necessary to ensure that the mold can produce filters with high-precision filtration pores and also consider the stability and durability of the filter under high temperatures, high pressures, and harsh chemical environments. Therefore, the structural design of the mold must be sophisticated and reasonable to achieve an efficient production process and high-quality product quality.
The selection of materials plays a decisive role in the quality and lifespan of filter molds. Usually, high-strength, wear-resistant, and high-temperature-resistant alloy steels or hard alloys are selected for mold manufacturing. These materials have excellent mechanical properties and can withstand the frequent opening and closing of the mold and the huge pressure and friction brought about by the high-pressure injection molding process. For instance, in some high-precision filter molds, specially heat-treated mold steels are used to increase their hardness and wear resistance, thereby ensuring that the mold can still maintain precise dimensions and shapes after long-term use.
The manufacturing process is the key link in creating high-quality filter molds. Modern mold manufacturing widely adopts advanced CNC processing technologies, such as CNC milling machines, electrical discharge machining, and wire cutting. These technologies can precisely transform complex mold designs into actual mold parts, achieving processing accuracy at the micrometer or even nanometer level. In terms of the surface treatment of molds, processes such as chrome plating and nitriding are usually employed to increase the hardness and smoothness of the mold surface, reduce the demolding resistance of the product, and improve the surface quality of the filter.
During the use of filter molds, correct operation and maintenance are crucial. Operators need to strictly follow the operating procedures for production to avoid mold damage caused by improper operation. For example, during the injection molding process, it is necessary to control the injection pressure and temperature to prevent excessive pressure and temperature from causing damage to the mold. At the same time, regular maintenance is also essential. After each use, residual materials and oil stains on the mold surface should be promptly cleaned to prevent corrosion of the mold surface. Regular inspections of the guiding components, ejection mechanisms, and cooling systems of the mold should be conducted to ensure their normal operation.
For the quality inspection of filter molds, high-precision measuring equipment such as coordinate measuring machines and projectors are typically used to inspect the key dimensions and geometrical tolerances of the molds to ensure they meet the design requirements. In addition, through trial mold production, the appearance, dimensional accuracy, and filtration performance of the filter products are inspected to promptly detect and solve potential problems in the mold.
With the advent of the Industry 4.0 era, the manufacturing of filter molds is also continuously integrating intelligent and digital technologies. Through computer simulation and emulation technologies, potential problems can be predicted and optimized during the mold design stage. Data collection and monitoring systems in the mold manufacturing process can grasp the production progress and quality status in real-time, achieving refined management.
In the future, with the continuous development of filtration technology and the continuous expansion of application fields, the requirements for filter molds will also become increasingly higher. Mold manufacturers need to continuously innovate, improve the manufacturing accuracy and efficiency of molds, and develop more advanced materials and processes to meet the market's demand for high-quality filters.
In conclusion, as the core equipment for filter production, the technical level and quality of filter molds directly affect the development of the filter industry. Only by constantly pursuing excellence can one remain invincible in the fierce market competition and provide various fields with more high-quality and efficient filtration solutions.
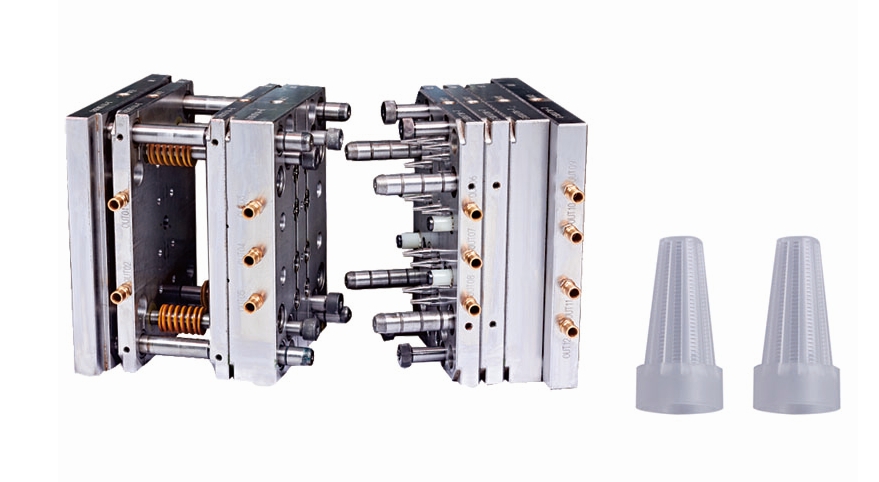
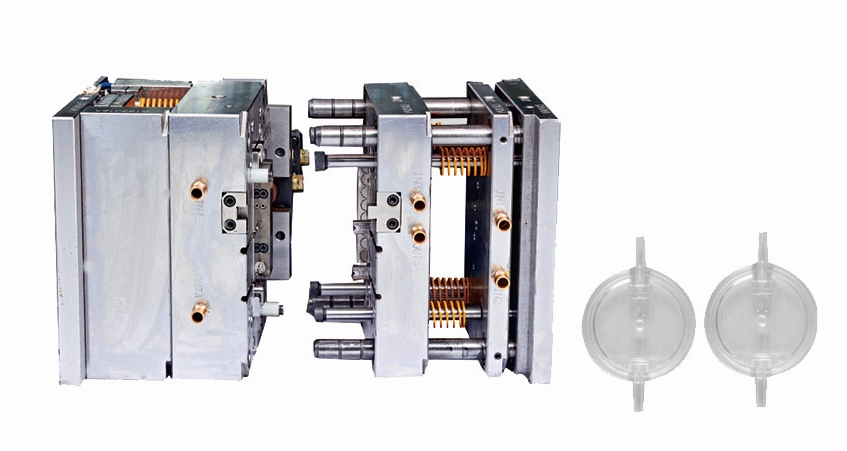
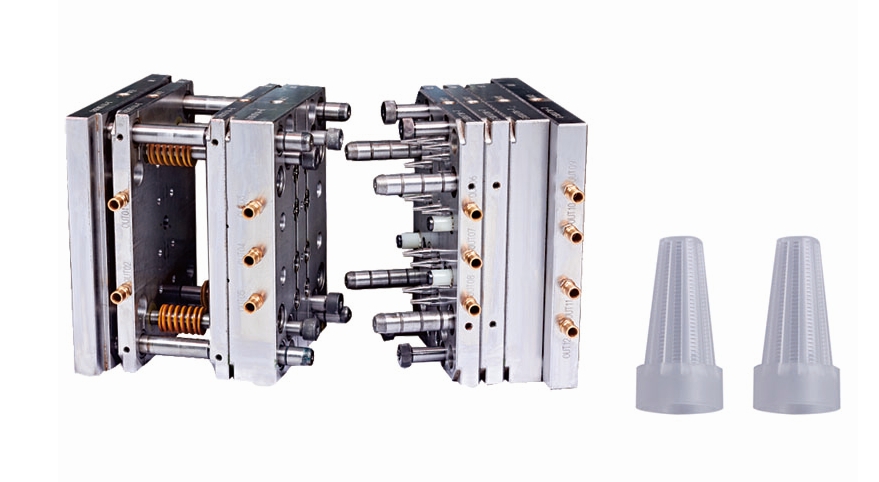
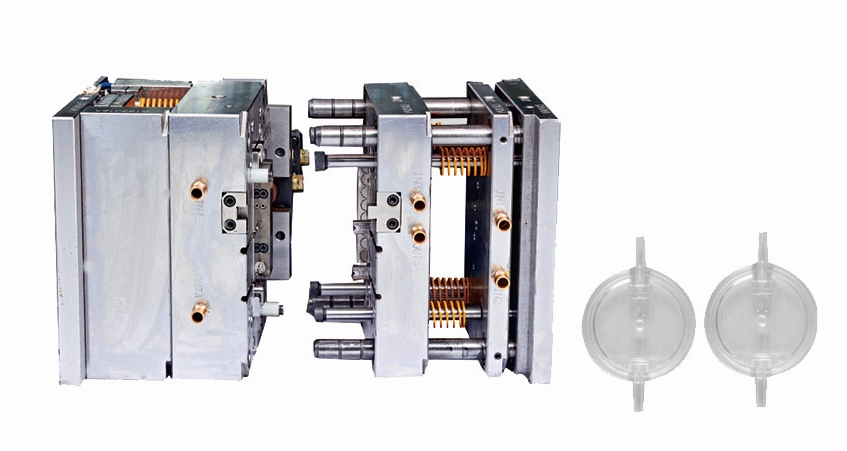
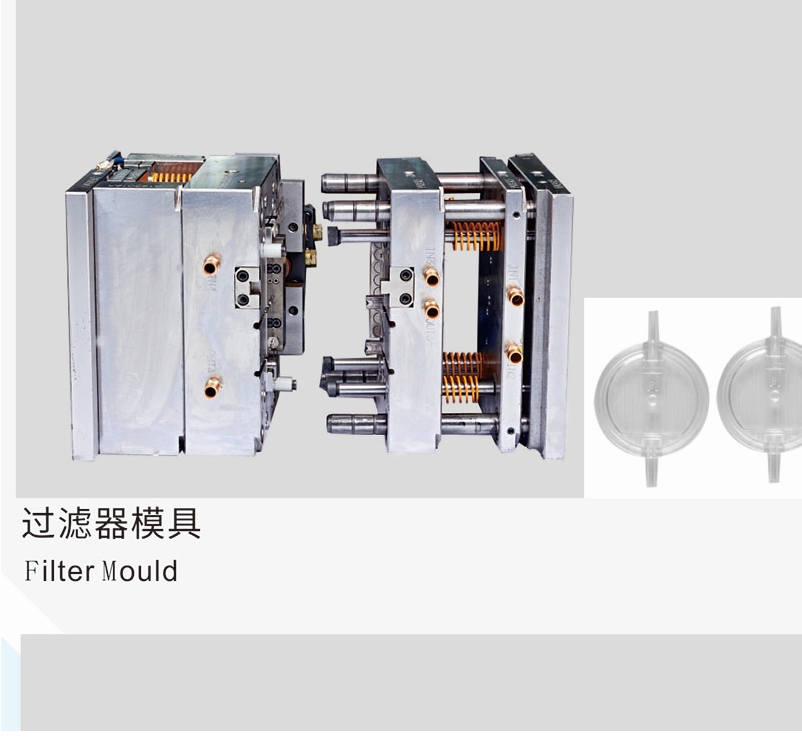
Related Keywords
Related Keywords