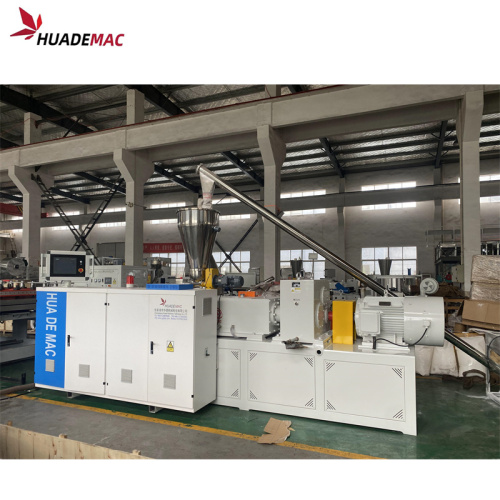
good quality 1220mm PVC /WPC foam board production line
-
$120000.001-2 Set/Sets
-
$110000.00≥3 Set/Sets
- Transportation:
- Ocean
- Port:
- shanghai
Your message must be between 20 to 2000 characters
Contact NowSupply Ability: | 10 |
---|---|
Payment Type: | T/T,L/C |
Incoterm: | CFR |
Transportation: | Ocean |
Port: | shanghai |
A WPC (Wood Plastic Composite) PVC foam board extrusion line is a manufacturing process used to produce composite boards that combine wood and plastic components, often with the addition of foam for enhanced properties. This type of line is typically used in industries such as construction, furniture making, and packaging due to its durability, moisture resistance, and eco-friendliness.
The process generally involves several key steps:
1. *Material Preparation*: Raw materials such as wood flour, recycled wood chips, and plastic pellets (usually polyvinyl chloride or PVC) are mixed together in a compounder. This mixture is then processed to create a homogenous blend that can be easily worked into the desired shape.
2. *Blowing Agent Addition*: To create a foam board, a blowing agent is added to the mixture during this stage. The blowing agent is usually a chemical that releases gas when heated, causing the mixture to expand and form a foam structure.
3. *Extrusion*: The blended and expanded material is then fed into an extruder, a long barrel with a screw mechanism that pushes the material through a die. The high pressure and temperature ensure that the material is shaped correctly as it exits the die.
4. *Cooling and Solidification*: Once the material has passed through the die, it is cooled rapidly to solidify the foam structure. This could involve passing the extruded material through a water bath or using air cooling systems.
5. *Cutting and Processing*: The extruded foam board is then cut to the desired size and shape. Additional processing may include edge trimming, surface finishing, and marking.
6. *Quality Control*: Finally, the boards undergo quality control checks to ensure they meet the required standards for thickness, density, and other specifications.

Related Keywords