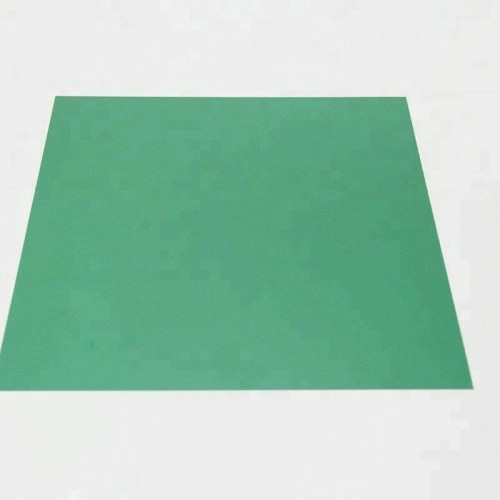
conventional postive ps plate carrier setup
- Transportation:
- Ocean, Land, Air
- Port:
- ShangHai Port, Ningbo Port
Your message must be between 20 to 2000 characters
Contact NowPlace of Origin: | China |
---|---|
Supply Ability: | Strong |
Payment Type: | L/C,T/T,D/P |
Incoterm: | FOB,CFR,CIF,EXW |
Transportation: | Ocean,Land,Air |
Port: | ShangHai Port,Ningbo Port |
Maintain good printing effect
The characteristics of Conventional Positive Ps Plate Covers are: the place with words has strong water repellence, and the place without words has strong water affinity. In this way, when printing Conventional Positive Ps Plate Check, there is ink on the word, and there is no ink on the word blank, and then printing ink on the blanket by Conventional Postive Ps Plate Design, Then transfer to business card paper through rubber cloth. Therefore, it is very important to keep the balance of water and ink in the printing process, which is also the key to printing a good business card.
Exposure exposure is to attach the photosensitive layer of the positive photo negative film with the film layer and the photosensitive layer of the positive photo PS version to a vacuum in the printing machine. After setting the printing process parameters, the printing machine is turned on. The light source (ultraviolet-rich iodine lamp) exposes the printing plate, and the photosensitive layer in the blank part undergoes a photolysis reaction under the irradiation of light.
Development and development is to develop the exposed PS plate with dilute alkali solution (5% NaOH solution) on the plate processor, so that the compounds generated by the decomposition of visible light are dissolved, and the photosensitive layer without visible light is left on the plate. , forming a lipophilic graphic part.
Decontamination and repair Decontamination is to use a decontamination liquid to remove the excess rule lines, glue lines and traces left by the edge of the positive negative film on the layout, as well as dust and dirt. Repair is to use repair solution to supplement and repair the graphics (such as lines, text, etc.) lost on the PS plate after development due to various reasons.
Baking plate Baking plate is the printing plate after exposure, development, decontamination and repair, after coating the surface with protective liquid, put it in the plate baking machine, and bake it at a constant temperature of 230-250 ℃ for 5- 8min, take out the printing plate, after natural cooling, develop it again with the developer, and clear the remaining protective liquid on the plate, and finally dry it with hot air. By baking the plate, the endurance of the PS plate can be increased by 50,000-100,000 impressions.
Ink extraction Ink extraction is to coat the developed black ink on the graphic part of the printing plate, which can increase the adsorption of the graphic photosensitive layer to the ink, and also facilitates the inspection of the printing quality.
Gluing Gluing is to coat a layer of gum arabic on the surface of the printing plate, which makes the hydrophilicity of the non-graphic blank
YP-II POSITIVE PS PLATE |
|
Plate type |
Positive |
Application |
Commercial sheetfed and rotary press printing |
Substrate |
Electro-chemically grained and anodized lithographic aluminum. |
Gauge |
0.15/0.25/0.30/0.40mm |
Maximum width |
1320mm |
Spectrum scope |
350-420nm |
Sensitivity |
130-150mj/cm2 |
Safe light |
UV filtered or Yellow light |
Coating color |
Green |
Dot reproduction |
2%-98%@ 200lpi Depend upon capability of imaging device |
Run length |
Above 100,000 |
Developer |
Huaguang PD developer (concentrated solution), |
Development |
1 liter can process 15 sqm Developer dilute ratio: 1:4(machine)-1:6(hand) Developing Temperature: 24-26℃ Developing Time: 20-30secs |
Packaging |
0.15mm 100 pieces/box 0.25/0.30mm 50 pieces/box if length <1030mm; 30 pieces/box if length ≥1030mm; 25 pieces/box if the area > 1m2 |
Related Keywords