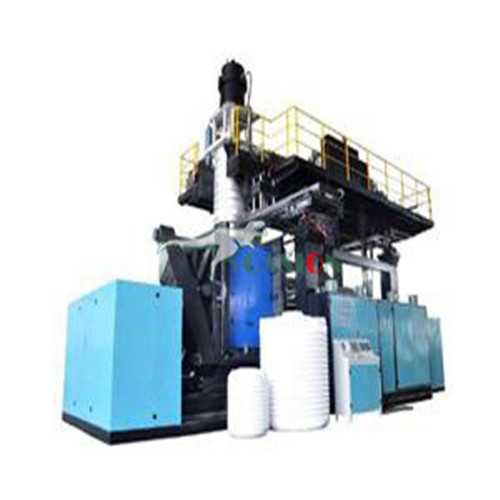
Plastic Water Bucket Blow Molding Machine
- Payment Type:
- T/T
- Incoterm:
- FOB, CIF
- Min. Order:
- 1 Set/Sets
- Min. Order:
- 1 Set/Sets
- Delivery Time:
- 60 Days
- Transportation:
- Ocean, Land
Your message must be between 20 to 2000 characters
Contact NowPlace of Origin: | china |
---|---|
Payment Type: | T/T |
Incoterm: | FOB,CIF |
Transportation: | Ocean,Land |
Automatic Blow Molding Machine
Configuration of Injection-Blowing Machine :
1. Oil pump and hydraulic valve (Directional Valves, Power saving valves, Pilot operated check modular valves, and Throttle&check modular valves ): YUKEN brand Ex Japan.
2. Pneumatic valve connector: FESTO Ex Germany.
3. Hydraulic pressure hose: ISR brand Ex USA.
4. Oil seal: VALQUA brand Ex Japan.
5. Hydraulic Motor: INTERMOT brand Ex Italy or SAMUN brand.
6. Controlling system: JINGHUA brand Ex Taiwan.
7. Electronic Rulers: NOVOTECHNIK brand Ex Germany
8. Moulded case circuit breaker, contactor, Thermal overload relay: SCHEIDER brand Ex France.
9. No fuse breaker: SCHNEIDER -MERLIN GERIN
10. Proximity Sensor: FOTEK brand Ex Taiwan.
11. Digital controller: RKC brand Ex Japan.
12. Conveyer motor: TONG WAY TEAM brand Ex Taiwan.
13. Electric Motor: Siemens bran
KHX-260-120
Technical Data forBlow Molding KHX-260-120
1. General Issues
Machineoperating manual including Hydraulic, Pneumatic, Assembly drawing, Coolingwater.
Max.volume of product: single cavity 260L Total weight 35 ton 3.5-4.5bars
Max. output 20pcs/h (220L product net weight 10.5Kg,Sufficientcooling water temperature at
8ºC with an intake pressure of between3.5 to 4.5 bars, with a Min. difference between intake and outlet of 3 bars. )
2. Clamping Unit
Principle: bi-direction synchronous clampingdevice with double axis.
Linearroller guidance horizontal.
Clampingforce: 750KN
Moldplatens H x W 1500 x 1000 mm
Distancebetween the p;atens: 750-1750mm
Clampingunit stroke: 1000mm
3. Die Head
Typeof die head: Double lays head of accumulator.
Max mouth diameter: 180-400MM
Max.Storage volume: 20L
Typeof temperature sensors: K
Heaterpower: 52KW
100point WPS systerm controller (B&R)
4. Extruder System
Extrudershould be adequate to work with HDPE
Screwdiameter: 120/30D
Nitridetreatment barrel and screw.
Plasticizingefficiency: 400 kg/h (HDPE)
Feedingzone grooved with cooling water
Cast-aluminium heater, adopt European mode ofconnection
Typeof temperature sensors:
DC motor drive: 132KW
Coolingby 5 cooling fans.
Raw material hopper with awindow.
5.BlowSystem
Blowsystem mounted on linear guide under the mold.
Heightadjustment mechainsm 250 mm
Blow pin up/down stroke: 150 mm , controlledby hydraulic cylinder
Parison closed
Mechanical adjustment for left and right
6. Take out system
Takeout stroke 1600 mm
Adopt lear guide and synchronous belttransmission of motor to advance and retreat
Gripper with the function: auto coolingwater
7. Hydraulic System
Hydraulic working pressure 100 -150 bar
Hydraulicsystem servo pump : 220 L/min
Hydraulicvalves:Yuken brand
Oil Temperature sensor showing the screen
Motor power: 22KW
Servosystem
Servovalve: (REXROTH--FromGermany)
Servooil source:4KW
Pistonpump:YUken (YUKEN--From Japan)
Threads ofhydraulic block use of screw joint GE(ISO 1179)
8. Pneumatic System
Pneumaticcylinders AIRTEC
Pneumatic valves AIRTEC
Max. pressure of all components: 10 bar
Max. pressure of gauge: 6-8bar
9.Control System
ControlSystem:B&R
B&R100point.
ServoWDS control system: B&R100point.
Full color 12.4"
Fullcolor 12.4" screen.
Recipeand machine data storage on memory stick (CF)
Emergencystop push buttons (rotationally release) without key
Allelectric components needs to be for power supply 220V/380V, 50Hz, controllerDC24V,
Total rated power: 276 KW
Average energy consumption: 110 KW
Main components(Air switch, Contactor) :Schneider intermediate relay: Schneider
Invertot of extuder motor: PARK
Linear transducer: Gefran
Proximity switch:Schneider
Cooling water
Allpipes for cooling water made of rubber material.
Separatecooling water circuit for Mold, Blow pin, Extruder feeding zone, Oil cooling.
Waterconsumptions: 20m3/h
11.Machine frame
Clamping unit should beforward: 600 mm, for mold changing
Aluminum profiles for safety doors, with plastic window.
Machinecolor: according requirement of customer
Overall dimensions ofmachine LxWxH: 5.5 x 6.5 x 3.6 m
Related Keywords