
Fe-Cr-Al Alloy Foil Strip
- Delivery Time:
- 30 Days
Your message must be between 20 to 2000 characters
Contact NowPlace of Origin: | Jiangsu, China (Mainland) |
---|
2. Material: 1Cr13A14, 1Cr21A14, 0Cr21A16, etc
3. High load on the surface
The advantage of electric Fe-Cr-Al alloy: 1. Using high temperature in the atmosphere oCR27A17MO2 alloy of electric Fe-Cr-Al can be used up to 1400°C, while CR20NI80 alloy of electric Ni-Cr alloy can be usedup to 1200°C. 2. Using longer Using the same high temperature in the atmosphere, Fe-Cr-Al components can be used longer as 2 to 4 times as Ni-Cr components. 3. High load on the surface Fe-Cr-Al componentscan sustain high load on the surface because of its using high temperature and long-life usage. 4. Sound antioxidant Al203 oxide film generated on the surfaceof Fe-Cr-Al alloy is structure-compact and well adhesion with matrix, and melting point of Al203 determine Al203 oxide film excellent antioxiadnt. Carburization resistance is higher than Cr203 generated on the same components. 5. Low weight The weight of Fe-Cr-Al alloy is lower than Ni-Cr alloy, which means that using Fe-Cr-Al saves more materials than using Ni-Cr when production tha same components. 6. High resistivity The resistivity of Fe-Cr-Al alloy is higher than that of Ni-Cr alloy. In designing components, using large specification alloy is advanageous for prolonging its life, which is very inportant for narrow alloy wire, such as choosing materialswith the same specification, the higher resistivity the less material, the smaller place occupied in furnace. 7. Excellent anti-sulfur Fe-Cr-Ali can resist corrosion for sulfur atmosphere and material contamination, but Ni-Cr will will be subjsct to severe erosion.
Alloy Nomenclature Performance | 1Cr13Al4 | 0Cr25Al5 | 0Cr21Al6 | 0Cr23Al5 | 0Cr21Al4 | 0Cr21Al6Nb | 0Cr27Al7Mo2 | |
Main Chemical composition | Cr | 12.0-15.0 | 23.0-26.0 | 19.0-22.0 | 20.5-23.5 | 18.0-21.0 | 21.0-23.0 | 26.5-27.8 |
Al | 4.0-6.0 | 4.5-6.5 | 5.0-7.0 | 4.2-5.3 | 3.0-4.2 | 5.0-7.0 | 6.0-7.0 | |
Re | opportune | opportune | opportune | opportune | opportune | opportune | opportune | |
Fe | Rest | Rest | Rest | Rest | Rest | Rest | Rest | |
|
|
|
|
|
| Nb0.5 | Mo1.8-2.2 | |
Max. continuous service temp. of element(°C) | 950 | 1250 | 1250 | 1250 | 1100 | 1350 | 1400 | |
Resistivity at 20ºC(μΩ·m) | 1.25 | 1.42 | 1.42 | 1.35 | 1.23 | 1.45 | 1.53 | |
Density(g/cm3) | 7.40 | 7.10 | 7.16 | 7.25 | 7.35 | 7.10 | 7.10 | |
Thermal conductivity(KJ/m·h·ºC) | 52.7 | 46.1 | 63.2 | 60.2 | 46.9 | 46.1 |
| |
Coefficient of lines expansion(α×10-6/ºC) | 15.4 | 16.0 | 14.7 | 15.0 | 13.5 | 16.0 | 16.0 | |
Melting point approx.( ºC) | 1450 | 1500 | 1500 | 1500 | 1500 | 1510 | 1520 | |
Tensile strength(N/mm2) | 580-680 | 630-780 | 630-780 | 630-780 | 600-700 | 650-800 | 680-830 | |
Elongation at rupture(%) | >16 | >12 | >12 | >12 | >12 | >12 | >10 | |
Variation of area(%) | 65-75 | 60-75 | 65-75 | 65-75 | 65-75 | 65-75 | 65-75 | |
Repeat Bending frequency(F/R) | >5 | >5 | >5 | >5 | >5 | >5 | >5 | |
Hardness(H.B.) | 200-260 | 200-260 | 200-260 | 200-260 | 200-260 | 200-260 | 200-260 | |
continuous servicetime(Hours/ ºC) | -- | ≥80/1300 | ≥80/1300 | ≥80/1300 | ≥80/1250 | ≥50/1350 | ≥50/1350 | |
Micrographic structure | Ferrite | Ferrite | Ferrite | Ferrite | Ferrite | Ferrite | Ferrite | |
Magnetic properties | Magnetic | Magnetic | Magnetic | Magnetic | Magnetic | Magnetic | Magnetic |
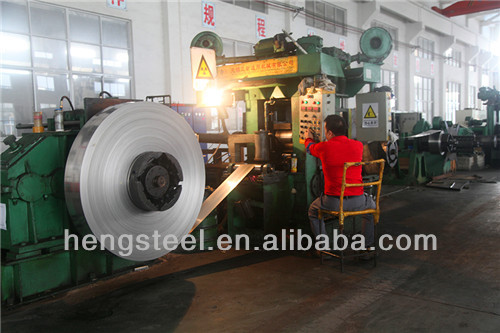
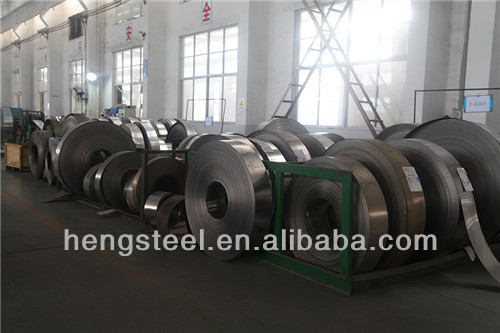
Related Keywords