
Sheet Glass Production Line (Plant)
- Payment Type:
- L/C, T/T, D/P, Western Union
Quantity:
Your message must be between 20 to 2000 characters
Contact NowBasic Info
Basic Info
Place of Origin: | Jiangsu Suzhou |
---|---|
Payment Type: | L/C, T/T, D/P, Western Union |
Product Description
Product Description
We can design the production line according to your requirements. The following data is just for your refernence.
1. Main Technical and economic index of production line.
2.Sheet Glass Equipments List Supplied by The Seller.
3. Process flow
(1)The batch prepared by raw material workshop is transported to the bin at the head of the furnace by the batch belt, one feeder under the bin are installed to push the batch uniformly to the furnace for melting purpose.
(2)Furnace using natural gas as fuel. Natural gas by spray gun into the furnace, the combustion air via the air exchanger by reversing, the branch flue into the regenerator, after injection into the furnace and gas burning heating furnace after the mixing of small batch and glass liquid.
(3)The batch turns into glass metal after melting, and it enters the molding room through the channel after the process of clarity, uniformity and cooling, and it is molded after pulling and finally enters into the annealing lehr.
(4)After entering into the annealing lehr, glass belt will go through the processes of heating, symmetrical heating, heat preservation, slow cooling and rapid cooling etc. This is to reduce the internal stress produced during the process of molding and cooling to meet the quality requirement of cutting. At last the temperature of glass belt falls to about 70ºC and then it is transported into the cutting zone.
(5)After the glass ribbon is out of the annealing lehr, it will go through the operation of automatically cutting, severing etc. The glass after severing shall enter into the acceleration separation roller for separation and then get into the process of edge severing. After manually collecting and packaging, the qualified glass will be transported to the finished product warehouse by forktruck. A cullet bin is installed under the edge severing section of the production line to collect the cullet. And it will be transported to the cullet load material system by trucks and then delivered to the bin at the head of the furnace.
4.Pictures
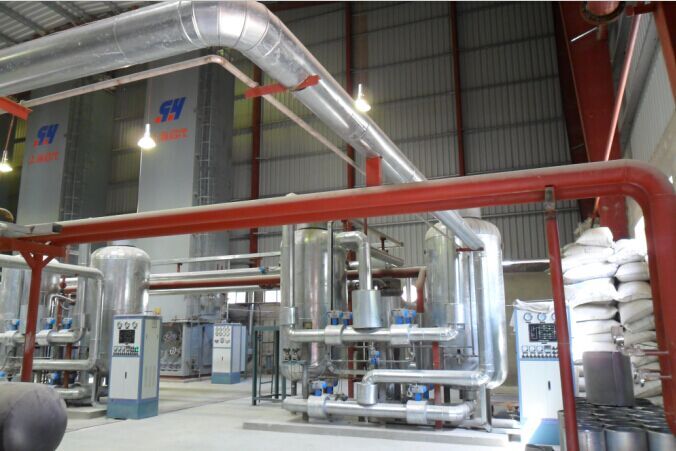
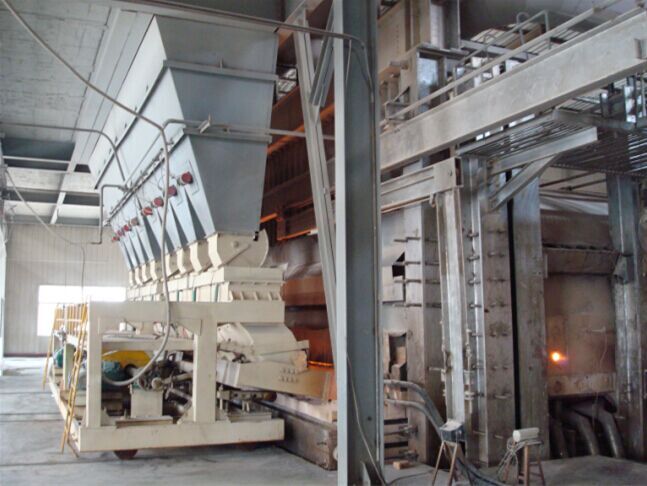

For more information, please contact us at any time.
1. Main Technical and economic index of production line.
No. |
Name |
unit |
Quantity |
Remark |
1 |
Production |
|||
1.1 |
Melting capacity |
t/d | 30 | |
1.2 |
Total pulling capacity |
t/d | 30 | |
1.3 |
Daily output |
t/d | 22.5 | 2250 m2/d(4mm) |
2 |
Process technical index |
|||
2.1 |
Gross ribbon width |
mm | 2200 | |
2.2 |
Net width |
mm | 1830 | |
2.3 | Thickness | mm | 1.8~8 | |
2.4 |
Total rate for made-up articles |
% | 75 | |
2.5 | Production cycle | a | a | |
3 |
Main raw material dosage |
|||
3.1 |
Sandstone |
t/d | 18.0 | |
3.2 |
Soda |
t/d | 5.69 | |
3.3 |
Dolomite |
t/d | 4.76 | |
3.4 |
Feldspar |
t/d | 2.32 | |
3.5 |
Limestone |
t/d | 0.82 | |
3.6 |
Mirabilite |
t/d | 0.32 | |
3.7 |
Coal dust |
t/d | 0.018 | |
3.8 |
Cullet |
t/d | 6.775 | |
4 |
NG consumption |
|||
4.1 |
NG consumption |
Nm³/d | 6000 | Qnet=8400kcal/ Nm³ |
5 |
Compressed air consumption |
|||
5.1 |
Compressed air consumption |
Nm³/min | 9 | |
6 |
Total water consumption |
|||
6.1 | Circulating water | m³/d | 2440 | |
6.2 |
Fresh water |
m³/d | 70 | |
7 |
Power supply and distribution |
|||
7.1 |
Power consumption |
kW×h/d | 2200 | |
7.2 |
Total installed power |
kW | 500 | |
7.3 |
Installed power in normal production |
kW | 300 | |
8 |
Factory area |
|||
8.1 |
Factory area |
m*m | 80*150 |
2.Sheet Glass Equipments List Supplied by The Seller.
No. |
Name |
unit |
Quantity |
I |
Raw material workshop |
||
Scale |
set | 1 | |
belt conveyor |
pcs | 1 | |
permanent magnetic iron remover |
set |
1 |
|
mixer |
set | 2 | |
raw material and batch making electric control |
set | 1 | |
II |
united workshop |
||
1 |
furnace |
||
1.1 |
furnace refractory |
set | 1 |
1.2 |
steel structure of the furnace |
set | 1 |
2 |
process equipment of furnace |
||
2.1 |
exhaust emission system |
||
damper of main flue |
set | 1 | |
rotating damper |
set | 1 | |
air exchanger |
set | 2 | |
branch flue damper |
set | 2 | |
chain hoist |
set | 2 | |
2.3 |
other accessory equipments |
||
hopper wall vibrator |
set | 2 | |
single valve gate |
set | 2 | |
batch charger |
set | 2 | |
2.4 |
The electrical control cabinet of the above equipments. |
set | 1 |
2.5 |
Computer control system |
||
automatic reversing control |
set | 1 | |
temperature detecting system for the furnace |
set | 1 | |
linkage of batch charging and glass liquid elevation |
set | 1 | |
Thermal resistance and flowmeter thermocouple etc |
set | 1 | |
Detector of furnace pressure |
set | 1 | |
Measuring device of glass level |
set |
1 | |
Industrial television |
set | 2 | |
3 |
Annealing Lehr |
set | 1 |
4 |
shaping equipment |
set | 1 |
5 |
Annealing equipment |
set | 1 |
6 |
Cold End |
set | 1 |
III | |||
1 |
System of The natural gas |
set | 1 |
2 |
() Oil system (as standby) |
set | 1 |
IV |
fan system |
set | 1 |
V |
compressed air system |
set | 1 |
3. Process flow
(1)The batch prepared by raw material workshop is transported to the bin at the head of the furnace by the batch belt, one feeder under the bin are installed to push the batch uniformly to the furnace for melting purpose.
(2)Furnace using natural gas as fuel. Natural gas by spray gun into the furnace, the combustion air via the air exchanger by reversing, the branch flue into the regenerator, after injection into the furnace and gas burning heating furnace after the mixing of small batch and glass liquid.
(3)The batch turns into glass metal after melting, and it enters the molding room through the channel after the process of clarity, uniformity and cooling, and it is molded after pulling and finally enters into the annealing lehr.
(4)After entering into the annealing lehr, glass belt will go through the processes of heating, symmetrical heating, heat preservation, slow cooling and rapid cooling etc. This is to reduce the internal stress produced during the process of molding and cooling to meet the quality requirement of cutting. At last the temperature of glass belt falls to about 70ºC and then it is transported into the cutting zone.
(5)After the glass ribbon is out of the annealing lehr, it will go through the operation of automatically cutting, severing etc. The glass after severing shall enter into the acceleration separation roller for separation and then get into the process of edge severing. After manually collecting and packaging, the qualified glass will be transported to the finished product warehouse by forktruck. A cullet bin is installed under the edge severing section of the production line to collect the cullet. And it will be transported to the cullet load material system by trucks and then delivered to the bin at the head of the furnace.
4.Pictures
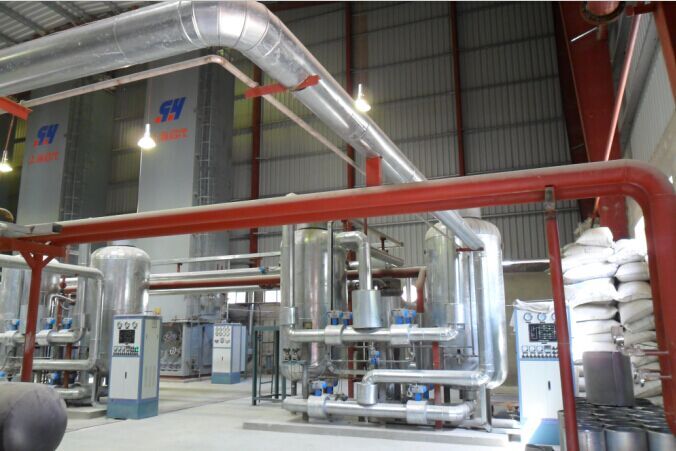
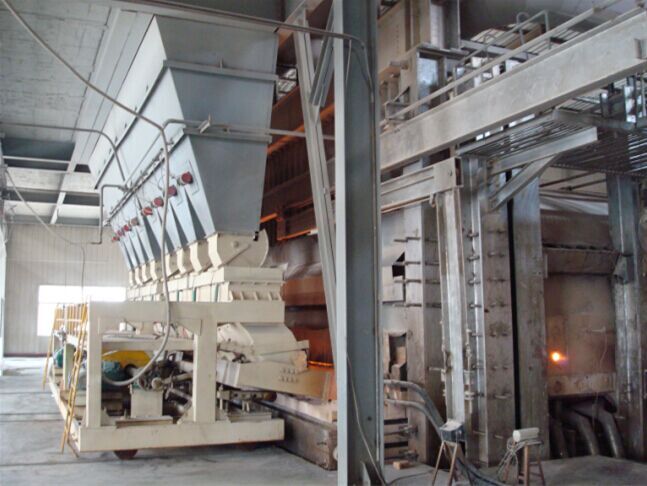

For more information, please contact us at any time.
Related Keywords
Related Keywords