
PCR Radial Single Stage Tyre Building Machine (LCZ-J1418B )
- Payment Type:
- L/C, T/T
Quantity:
Your message must be between 20 to 2000 characters
Contact NowBasic Info
Basic Info
Place of Origin: | jiangsu |
---|---|
Payment Type: | L/C, T/T |
Product Description
Product Description
Technical Parameters 1. Technical Parameters 14"-18"(13"-16", 16"-20", 20"-24")
2. Diameter of green tire min: Φ 475 max: Φ 800
3. Diameter of steel belt min: Φ 460 max: Φ 660
4. Diameter of carcass drum min: Φ 337 max: Φ 444
5. Carcass ply (adjustable according to the user)
- Width of inner-liner min: 280 max: 800
- Width of sidewall max: 260
- Sidewall/inner-liner composite min: 340 max: 1100
- Width of carcass ply min: 300 max: 800
6. Steel belt/tread (adjustable according to the user)
- Width of steel belt min: 80 max: 360
- Length of steel belt min: 1650 max: 2800
- Width of tread min: 200 max: 370
- Length of tread min: 1700 max: 2800
- Width of cap ply max: 380
7. Diameter of material rolls on the handcart
- Inner-liner, ply, sidewall, steel belt max: Φ 1000
- Tread max: Φ 1500
8. Device features
(1)Height of main shaft 950mm
(2)Drive of main shaft servo motor(200rpm)
(3)Unwound semi-product supply
- Inner-liner handcart
- 1st/2ND ply handcart
-Sidewall handcart
- Cap ply wooden shaft
(4)Semi-product length setting servo motor
(5)Semi-product centering CCD auto control
(6)Semi-product cutting auto cutting with heated knife and ultrasonic knife
(7)Semi-product splicing automatically
(8)Turn up/turn down bladder + bladder pushing ring
(9)Steel belt drum with double stations (steel belt + tread)
(10) Stitching combination stitching (TOS + SOT)
(11) Positioning servo motor + linearly displacement sensing
(12) Splicing roller multi-disk stitching roller
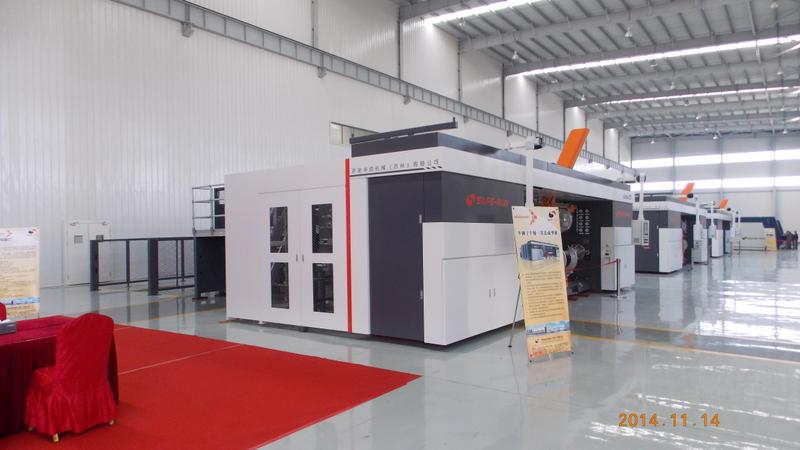
Brief Introduction
1. Servo drive is adopted for precise position of the main shaft. Linear displacement transducer is used to sense the drum's width. Servo + rack and pinion drive the transfer ring and clamping ring on the chasis. Linear displacement sensor is used to detect the location and the mechanical positioning with accurate repeatability and ensure the safety for both man and machine.
2. Main servicer and belt servicer adopt servo system and CCD auto rectifying system to realize the auto length setting, auto cutting, auto centering and auto splicing, so that the process circle time for the single tire has been minimized to 60 seconds (size 16" single carcass).
3. The cap ply winding adopts the Tension Control System which developed by our company ( applied for the national patent), the system ensures the tension of cap ply at 700± 200g and segmentation tension control is available.
4. The whole process is controlled by PLC(Programmable Logic Controller). The touch screen, human-machine interface, displays production procedure and provides processing parameter setting, sizes saving, fault diagnosing, and a convenient access to parameters and/or size changing, which is easy for you to operate.
5. Accurately machined parts give the machine good function and accuracy, as well as the guarantee of the green tire quality.
6. The production process and quality control meet ISO9001 standard.
2. Diameter of green tire min: Φ 475 max: Φ 800
3. Diameter of steel belt min: Φ 460 max: Φ 660
4. Diameter of carcass drum min: Φ 337 max: Φ 444
5. Carcass ply (adjustable according to the user)
- Width of inner-liner min: 280 max: 800
- Width of sidewall max: 260
- Sidewall/inner-liner composite min: 340 max: 1100
- Width of carcass ply min: 300 max: 800
6. Steel belt/tread (adjustable according to the user)
- Width of steel belt min: 80 max: 360
- Length of steel belt min: 1650 max: 2800
- Width of tread min: 200 max: 370
- Length of tread min: 1700 max: 2800
- Width of cap ply max: 380
7. Diameter of material rolls on the handcart
- Inner-liner, ply, sidewall, steel belt max: Φ 1000
- Tread max: Φ 1500
8. Device features
(1)Height of main shaft 950mm
(2)Drive of main shaft servo motor(200rpm)
(3)Unwound semi-product supply
- Inner-liner handcart
- 1st/2ND ply handcart
-Sidewall handcart
- Cap ply wooden shaft
(4)Semi-product length setting servo motor
(5)Semi-product centering CCD auto control
(6)Semi-product cutting auto cutting with heated knife and ultrasonic knife
(7)Semi-product splicing automatically
(8)Turn up/turn down bladder + bladder pushing ring
(9)Steel belt drum with double stations (steel belt + tread)
(10) Stitching combination stitching (TOS + SOT)
(11) Positioning servo motor + linearly displacement sensing
(12) Splicing roller multi-disk stitching roller
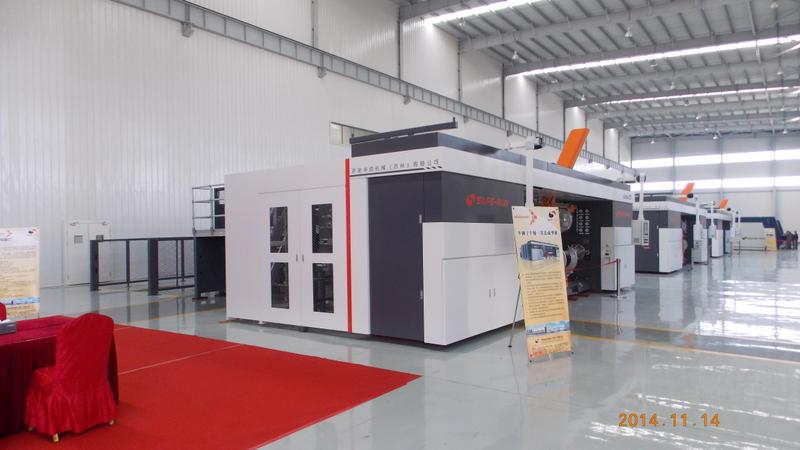
Brief Introduction
1. Servo drive is adopted for precise position of the main shaft. Linear displacement transducer is used to sense the drum's width. Servo + rack and pinion drive the transfer ring and clamping ring on the chasis. Linear displacement sensor is used to detect the location and the mechanical positioning with accurate repeatability and ensure the safety for both man and machine.
2. Main servicer and belt servicer adopt servo system and CCD auto rectifying system to realize the auto length setting, auto cutting, auto centering and auto splicing, so that the process circle time for the single tire has been minimized to 60 seconds (size 16" single carcass).
3. The cap ply winding adopts the Tension Control System which developed by our company ( applied for the national patent), the system ensures the tension of cap ply at 700± 200g and segmentation tension control is available.
4. The whole process is controlled by PLC(Programmable Logic Controller). The touch screen, human-machine interface, displays production procedure and provides processing parameter setting, sizes saving, fault diagnosing, and a convenient access to parameters and/or size changing, which is easy for you to operate.
5. Accurately machined parts give the machine good function and accuracy, as well as the guarantee of the green tire quality.
6. The production process and quality control meet ISO9001 standard.
Related Keywords
Related Keywords