
High Efficient PP PE Film Recycling Line
- Payment Type:
- L/C, T/T
Quantity:
Your message must be between 20 to 2000 characters
Contact NowBasic Info
Basic Info
Place of Origin: | Zhangjiagang, Jiangsu |
---|---|
Payment Type: | L/C, T/T |
Product Description
Product Description
High Efficient PP PE Film Recycling Line
Introduction
Δ Material: baled or loose PP/PE film/bag/woven bag
Δ Finished product size: 30-40mm
Δ Purpose of use: be used to making PP/PE granules
We can customize the washing line according to client's requirement.
Production Process
1. Size Reduction — 2. Friction Washing — 3. Washing & Density Separation
— 4. Moisture Removal — 5. Product Collecting
Technical Data
Model: ME-300
Δ Capacity: >300 KG Per Hour
Δ Installed Power: 122.9KW
Δ Hot Washing: Optional
Δ Water Supply: 2-3 Ton Per Hour
Δ Manpower: 3 Person
Δ Estimated line size: 28m*2.5m*3.5m
Main Machines & Function
Plastic Crusher (Wet Type)
Δ used for size reduction of the material into flakes
Δ special v-shape rotor design for film/bag crushing
Δ screen size: 100mm*20mm (length*width)
Δ output size: 30-40mm; capacity>300kg/hr (for film/bag/woven bag crushing)
Friction Washer
Δ used to scrubbing flakes by high speed blades to remove dirt and water
Δ rotary speed: 800rpm for high efficiency
Sink-Float Tank
Δ used to separating the sinkable contamination and cleaning the PP/PE flakes by rolling drums
Δ sink-float tank designed with 5pcs automatic drums on top for flakes automatic cleaning and conveying
Δ the side dirt lift screw conveyor is optional
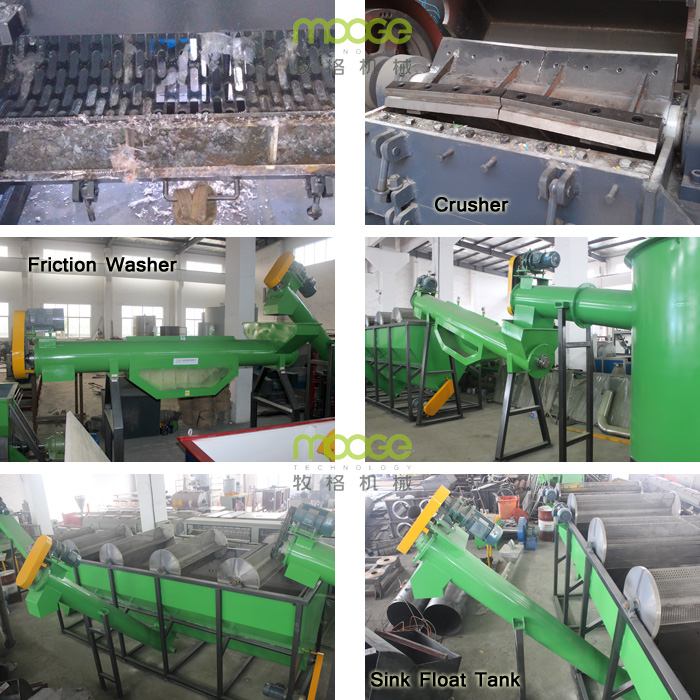
Dewatering Machine
Δ used for removal of the moisture from the flakes by high speed blades
Δ rotary speed: 1500rpm for high efficiency
Δ moisture content remain: 5-8%
Hot Air Dryer
Δ used for reducing moisture content from flakes by hot air
Δ moisture content remain: <3%
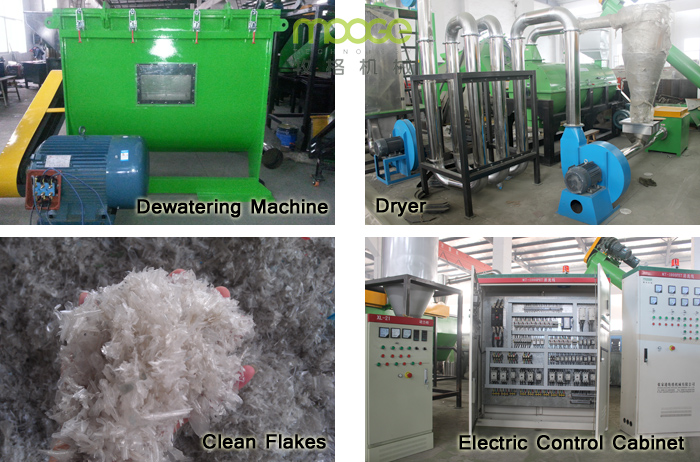
Optional Machine
Hot Washing Tank
Δ used to washing the flakes by hot water to remove glue and greasy dirt
Δ feeding caustic soda/detergent to wash
Δ heating by electricity or customized
Δ tank outside with heating protecting layer made of rockwool
Δ special design for PP/PE recycling
Introduction
Δ Material: baled or loose PP/PE film/bag/woven bag
Δ Finished product size: 30-40mm
Δ Purpose of use: be used to making PP/PE granules
We can customize the washing line according to client's requirement.
Production Process
1. Size Reduction — 2. Friction Washing — 3. Washing & Density Separation
— 4. Moisture Removal — 5. Product Collecting
Technical Data
Model: ME-300
Δ Capacity: >300 KG Per Hour
Δ Installed Power: 122.9KW
Δ Hot Washing: Optional
Δ Water Supply: 2-3 Ton Per Hour
Δ Manpower: 3 Person
Δ Estimated line size: 28m*2.5m*3.5m
Main Machines & Function
Plastic Crusher (Wet Type)
Δ used for size reduction of the material into flakes
Δ special v-shape rotor design for film/bag crushing
Δ screen size: 100mm*20mm (length*width)
Δ output size: 30-40mm; capacity>300kg/hr (for film/bag/woven bag crushing)
Friction Washer
Δ used to scrubbing flakes by high speed blades to remove dirt and water
Δ rotary speed: 800rpm for high efficiency
Sink-Float Tank
Δ used to separating the sinkable contamination and cleaning the PP/PE flakes by rolling drums
Δ sink-float tank designed with 5pcs automatic drums on top for flakes automatic cleaning and conveying
Δ the side dirt lift screw conveyor is optional
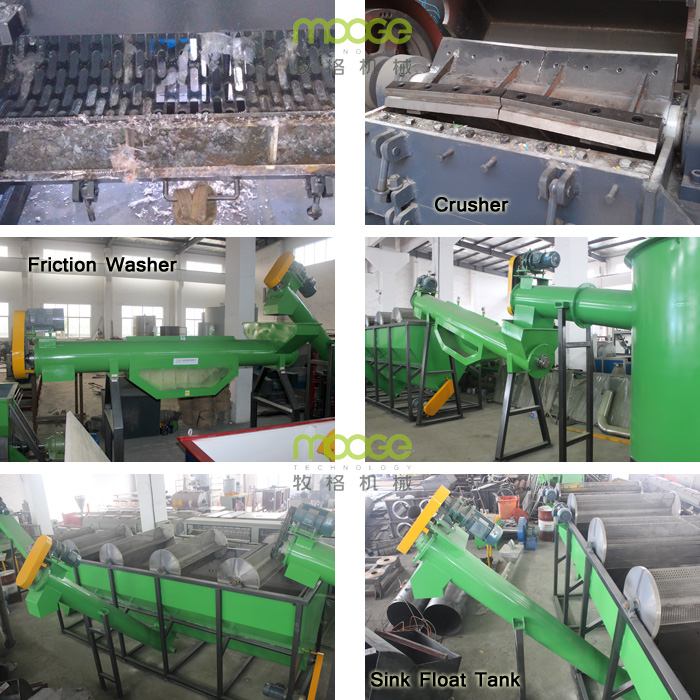
Dewatering Machine
Δ used for removal of the moisture from the flakes by high speed blades
Δ rotary speed: 1500rpm for high efficiency
Δ moisture content remain: 5-8%
Hot Air Dryer
Δ used for reducing moisture content from flakes by hot air
Δ moisture content remain: <3%
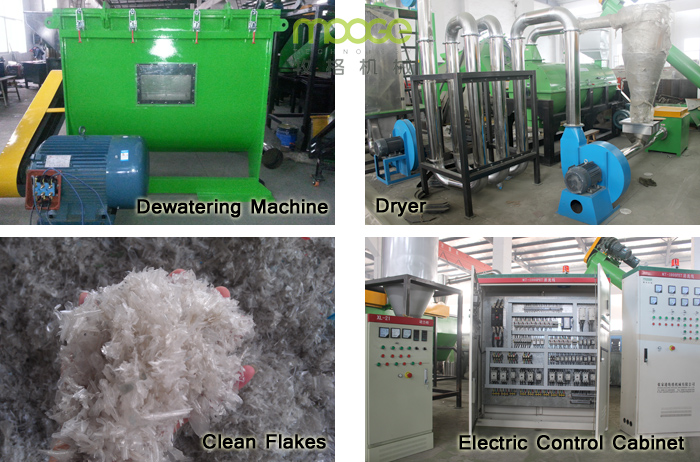
Optional Machine
Hot Washing Tank
Δ used to washing the flakes by hot water to remove glue and greasy dirt
Δ feeding caustic soda/detergent to wash
Δ heating by electricity or customized
Δ tank outside with heating protecting layer made of rockwool
Δ special design for PP/PE recycling
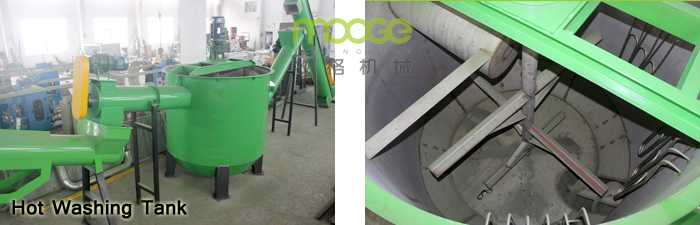
Related Keywords
Related Keywords